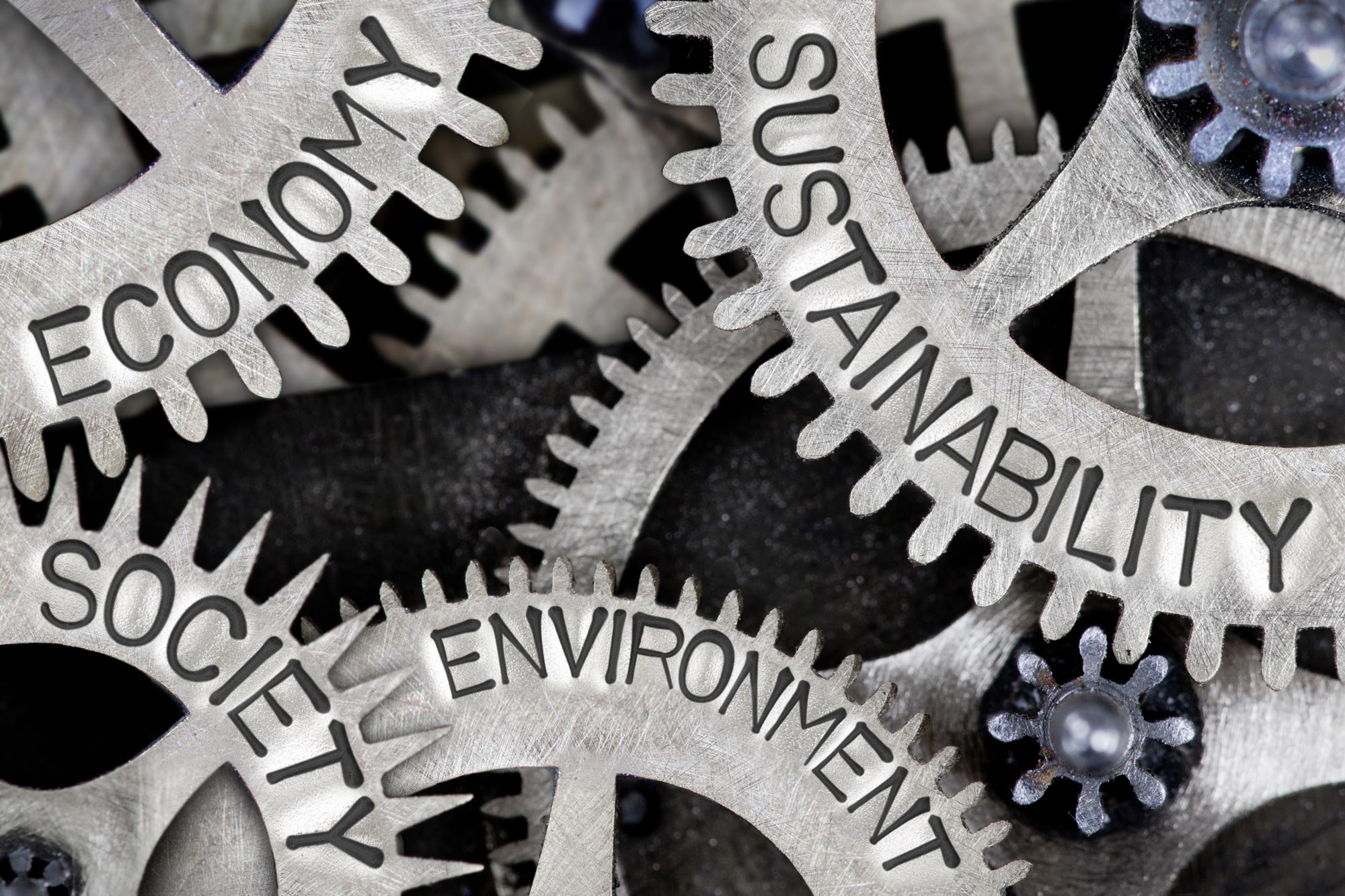
Why sustainable manufacturing makes economic as well as ethical sense
This article is brought to you thanks to the collaboration of The European Sting with the World Economic Forum.
Author: Derek O’Halloran, Head of Shaping the Future of Digital Economy and New Value Creation, World Economic Forum & Francisco D’Souza, Co-Founder, Cognizant; Fellow, World Economic Forum
The COVID-19 pandemic is simultaneously impacting global manufacturing demand and supply chains, workforce availability, energy use and CO2 emissions. Never before have we witnessed the drastic impact that reduced human activity can have on global emissions. In fact, global energy-related CO2 emissions are set to fall nearly 8% in 2020 to their lowest level in a decade. The UN advises global emissions must be cut to this same extent, each year, for the next decade to limit global warming to 1.5˚C.
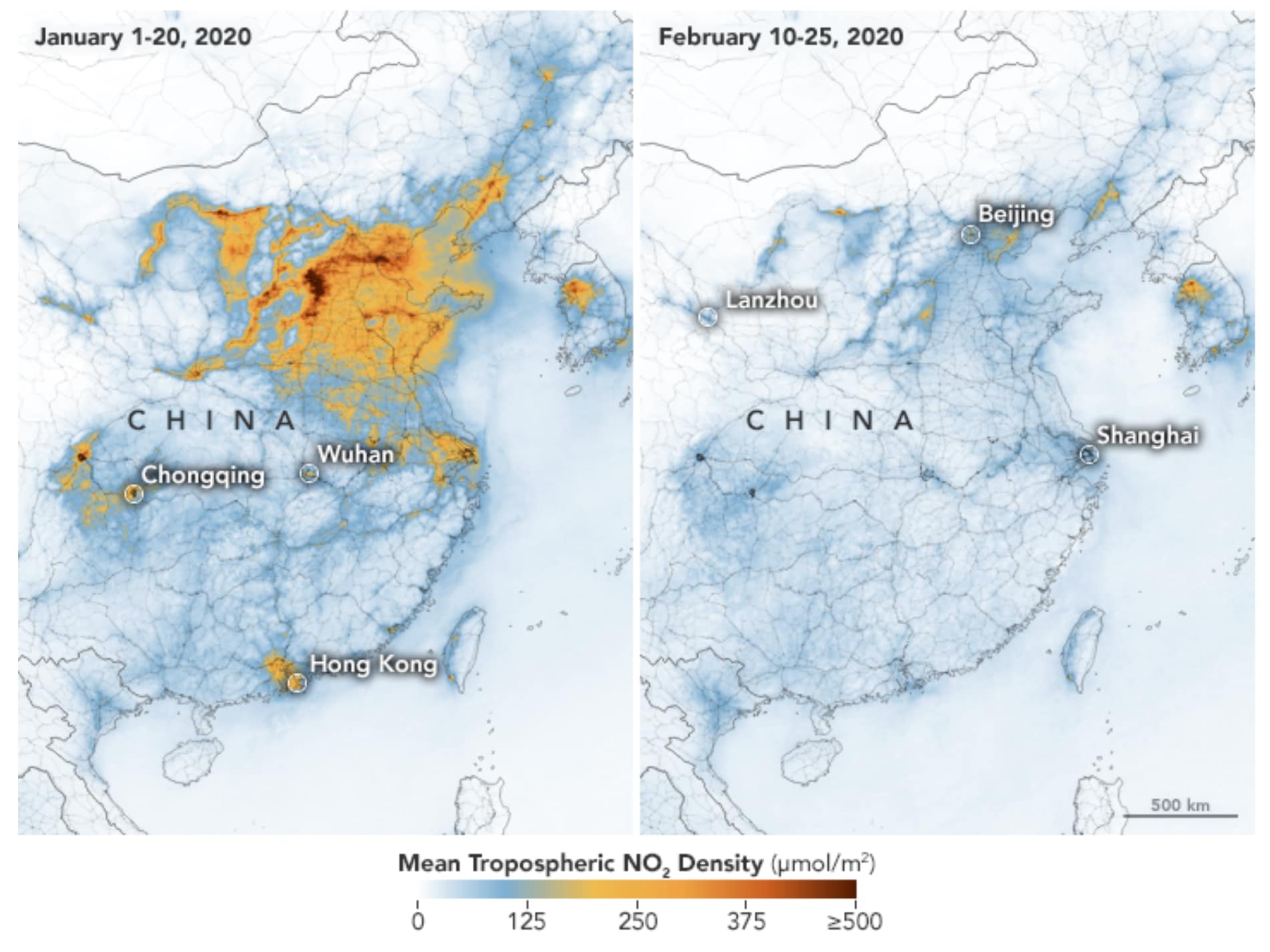
In purpose, there is hope
Over the past three months, manufacturing has been forced to change at an unprecedented rate, both to find ways to innovate given the scarcity of resources and to accelerate digital transformation.
The emissions reductions driven by crisis constraints is insightful and offers hope that dramatic change is possible – but we must act now. Given the abundance of resources, people will not be driven to innovate or challenge the status quo. By engineering within our planet’s constraints, industry can set the baseline for what must be considered and elevate what can be achieved – sustainably.
This begins with a rapid cultural narrative shift, already critical for consumer and next-generation workforce engagement – from business growth at the expense of people and nature, to a future that prioritizes the wellbeing of the planet.
Companies with a greater commitment to environmental, social and governance (ESG) benchmarking and reporting regimes continue to prove their ability to weather periods of uncertainty in the market better than their peers. According to a recent Blackrock report, despite the recent turmoil, companies with a record of good customer relations or robust corporate culture are demonstrating resilient financial performance. In fact, to date, more than 90% of sustainable indices have outperformed their parent benchmarks during the COVID-19 pandemic.
Resiliency through digital transformation
As a large consumer of energy, responsible for more than one-quarter of global CO2 emissions, industry must take a leading role fostering an economic recovery with sustainability as a business imperative. In reshaping our world toward a new normal, industry should leverage digital transformation at an accelerated pace. Typically leveraged for productivity, digital transformation is equally effective in achieving economic and environmental resilience.
To capitalize on the convergence of Industry 4.0 and ESG goals, industry leaders must enable operational efficiency, leverage renewable energy, practice life cycle thinking, and promote supply chain data transparency.
Enable operational efficiency
Most production facilities are passive participants in the global energy supply chain. They monitor overall energy use and costs associated with available sources, but often overlook the controllable factors inside operations that enable consumption management in a way that brings value to the business.
According to the 2019 World Energy Outlook by the International Energy Agency (IEA), “a sharp pick-up in efficiency improvements is the single most important element that brings the world towards the Sustainable Development Scenario”.
Manufacturers must evaluate and optimize individual, energy-intensive processes within operations by monitoring and measuring the process units, lines, and machines consuming energy, and then controlling overall consumption, economics and emissions.
Leverage renewable energy
The cost of renewable energy is driving its exponential adoption. Based on the levelized cost of energy, the cost of solar panels per watt produced in 1977 was $77; in 2020 it is $0.14.
Favorable economics paired with modern business models allow highly decentralized and digitized assets to be successful.
Digital technologies that enable bi-directional control and connectivity, when paired with distributed energy resources – such as solar plus battery storage – unlock new opportunities for flexible demand and curtailment. This includes peak load shedding, participation in automatic demand response management, buying and trading energy into the market, or dynamically shifting operations to match the availability of solar power and battery storage systems – for example, based on financial incentives and operational prioritization.
Practice life cycle thinking
Life cycle assessment (LCA) is an environmental framework that offers a holistic methodology for industry to assess the environmental impacts associated across the life stages of products.
Consider the life cycle of a vehicle. The current US vehicle emissions regulatory framework only focuses on a car while in its ‘fuel/energy use’ phase and does not address the emissions generated throughout its complete life cycle; this is extensive and involves raw material extraction, powertrain and components manufacturing, vehicle assembly, fuel cycle/energy use and end-of-life recycling and disposal.
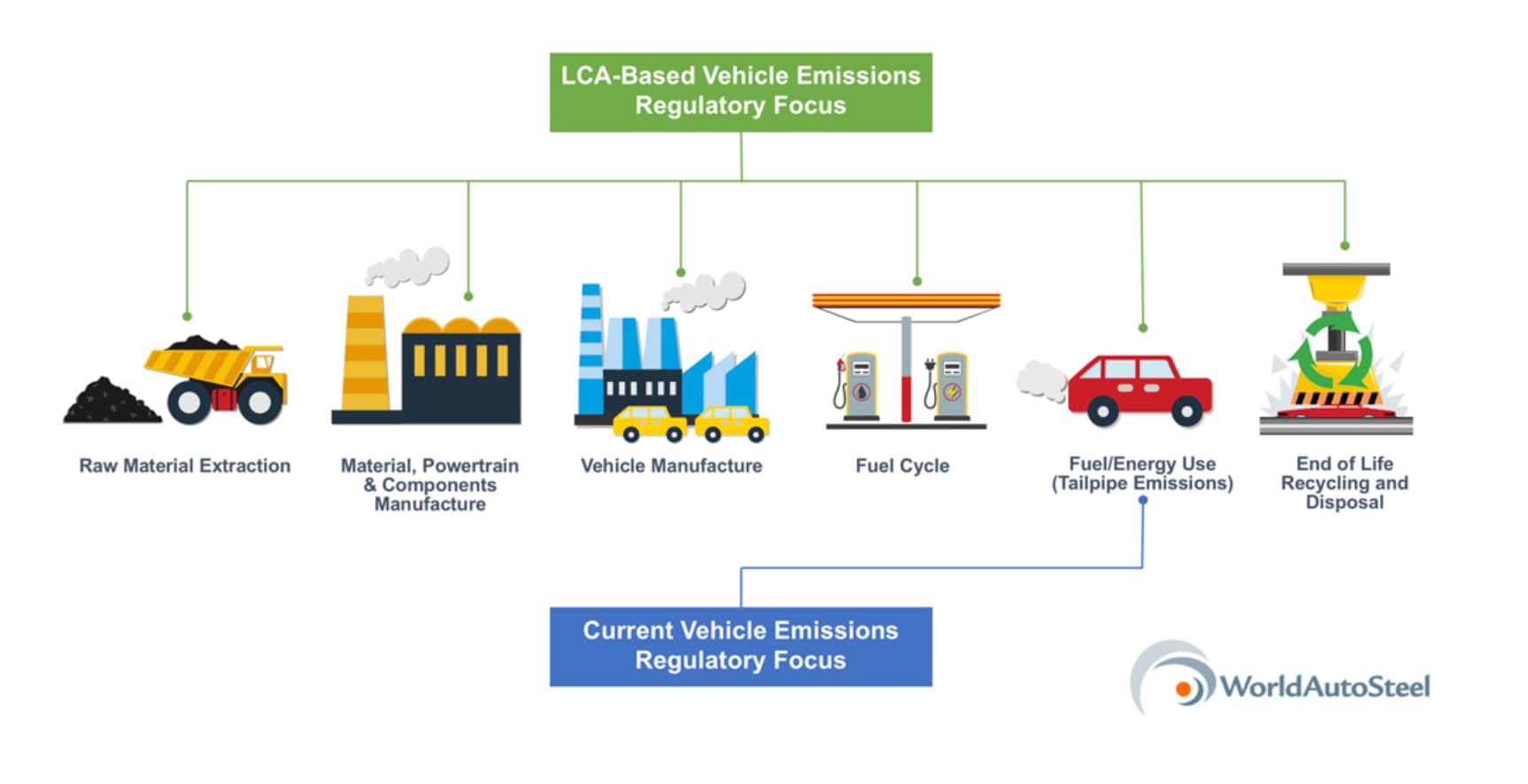
Nestlé, which has been taking a leading role in creating a net-zero recovery from COVID-19, conducted its first LCA over a decade ago to assess and minimize the impact of climate change at various stages across their supply chain. Following the study, Nespresso committed to reducing the carbon footprint of a cup of coffee by 28% by 2020. They have since increased the energy efficiency of their machines and have begun powering business operations with renewable energy.
Promote supply chain data transparency
The global supply chain is filled with inefficiencies and opportunities to greatly reduce waste.
Industrial symbiosis is one approach to a more sustainable and integrated industrial system. It establishes a network in which the waste from one process (such as materials, energy, water, capacity, expertise or assets) is used as a resource in another.
Developing global industrial symbiotic relationships means going beyond the traditional focus on internal operations and expanding to new business and business partnerships across the supply chain. These symbiotic communities engage diverse organizations in a network to foster eco-innovation and long-term culture change.
The Kalundborg Network, located in Denmark, is a noteworthy example of industrial symbiosis.
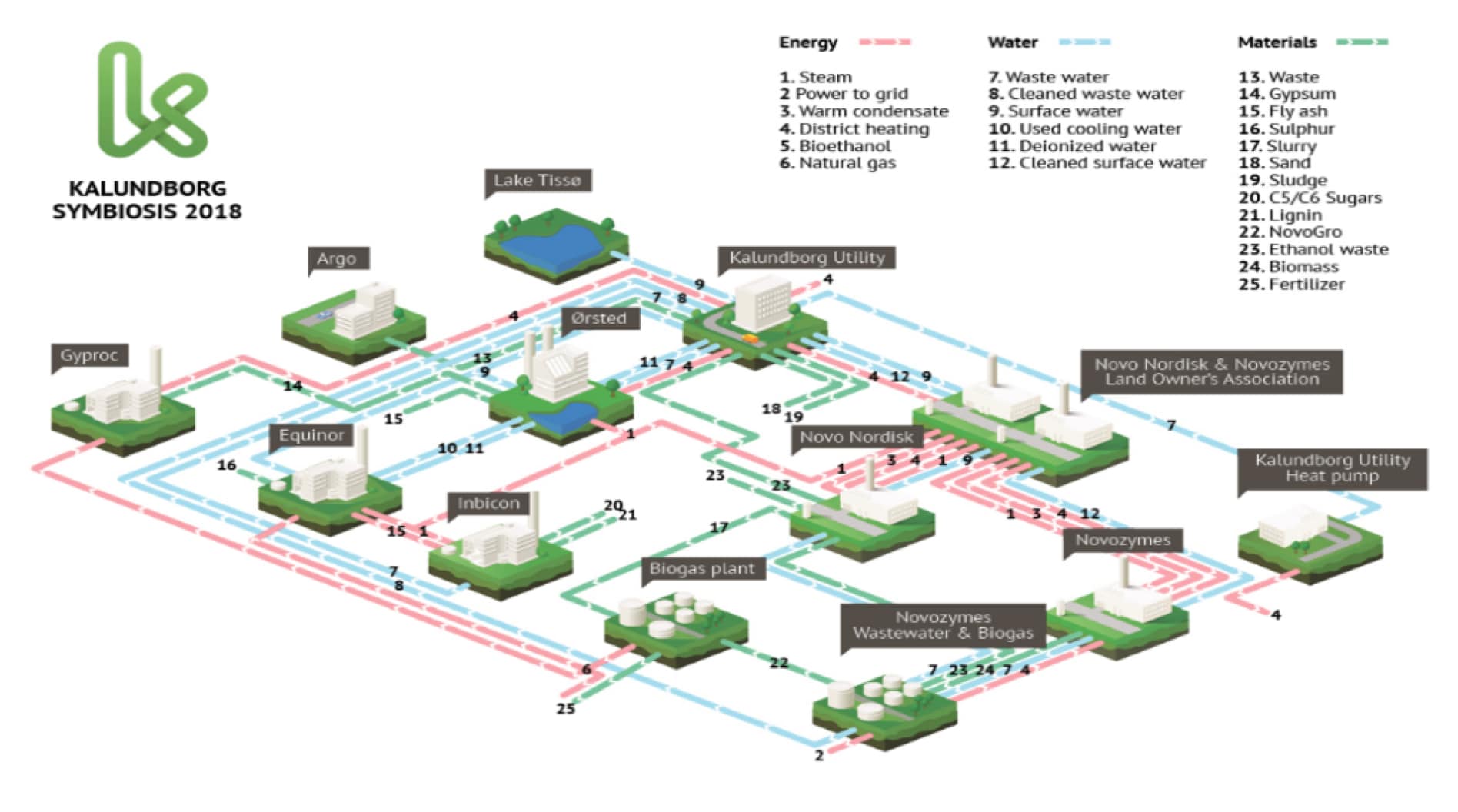
By collaborating, and exchanging material, water and energy streams between 11 public and private partners, the Kalundborg network increases resilience and economic gains for its members, while meeting ESG goals. Annually, combined benefits from the partners are 100GWh of energy, 635,000 tons of CO2, 3.6 million tons of water, and bottom-line savings of $24 million. This kind of symbiosis represents an immense opportunity for data transparency and the pairing of underused resources between companies.