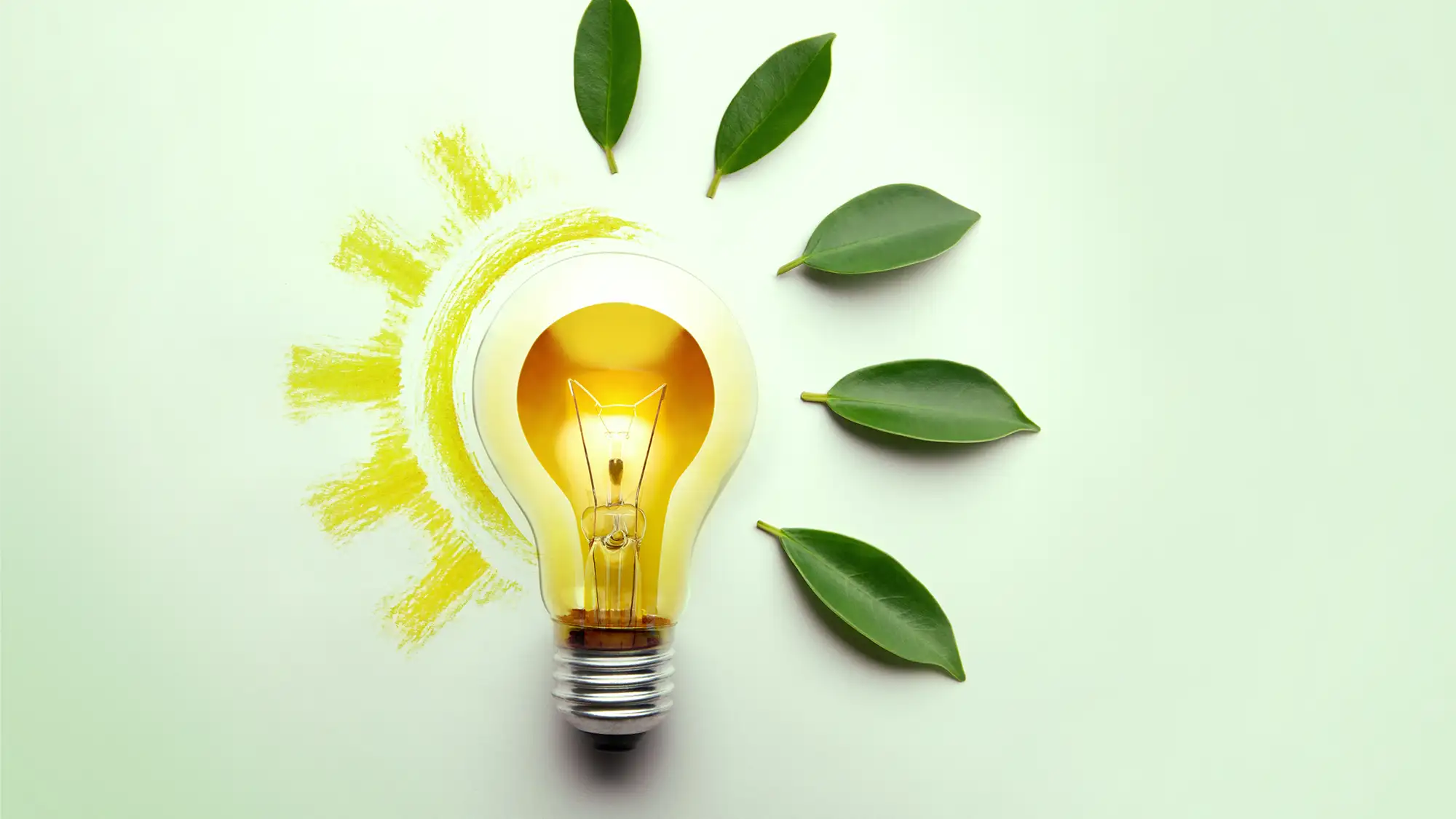
7 Inspiring Ideas for a more Sustainable Industry
The shift towards a more responsible industry is underway, and SEAM labeled members are leading the way. This month, we highlight 7 inspiring initiatives from our members, proving that ambitious CSR commitments are not only possible but also drive innovation and performance.
On the agenda: circular economy, carbon footprint reduction, waste management, supply chain engagement… Concrete levers to transform our industries and build a more sustainable future. On March 11, industry experts gathered at the SEAM workshop in Paris to discuss the SEAM Carbon Footprint Project and the best strategies to reduce greenhouse gas emissions. Get inspired and explore new initiatives to follow!
#1 CIRCULAR ECONOMY
Husqvarna Group is accelerating circular innovation, with 37 validated sustainable solutions by the end of 2024, and a goal of 50 by 2025.
Their strategy is based on the 5Rs of circularity:
✅ Reduce the use of natural resources
✅ Reuse components to extend product life
✅ Repair to minimize waste
✅ Refurbish used equipment
✅ Recycle to reintegrate materials at the end of life
With this approach, Husqvarna is proving that a circular model is not only possible but scalable and profitable.
#2 CARBON FOOTPRINT REDUCTION
Net Zero Emissions by 2050! Saint-Gobain Abrasives is actively reducing its carbon footprint across all three Scopes:
✅ Designing more sustainable products and materials
✅ Optimizing industrial processes and reducing energy consumption
✅ Partnering with suppliers and carriers to reduce emissions
One standout achievement: removing naphthalene from vitrified-bond abrasives productions, alongside other significant process optimizations – has proved a breakthrough that cut their carbon footprint while also improving safety and sustainability.
A clear example of how innovation and responsibility can drive meaningful change.
#3 WASTE MANAGEMENT
Mirka is introducing a new industrial process to Finland with the construction of an innovative circular grain manufacturing plant in Jeppo — the first of its kind globally. This investment supports the company’s continued role as a market shaper in the abrasives industry.
✅ €25 million investment in a circular grain manufacturing facility
✅ Expected to reduce CO₂ emissions by approximately 5,000 tons annually
✅ Launch of first circular abrasive products planned for 2026
#4 ECODESIGN BACKINGS
Ahlstrom is innovating in the abrasives industry with high-performance paper backing solutions developed under a Safe and Sustainable by Design approach:
✅ Formaldehyde-free backings
Since 2015, 100% of Ahlstrom’s abrasive backings have been formaldehyde-free, marking a major step forward for the workers.
✅ Sustainably sourced materials
All papers and composites are sourced from FSC® Controlled Wood as a minimum, ensuring sustainable forest management.
✅ Pioneering drop-in solutions for optimized supply-chain & less hazards use
- EZ-BOND drop-in solutions replacing post-saturated oil kraft papers, reducing hazards in the process
- TEX-STYLE™ offering a ready-to-use alternative to PES treated cloth, for some applications
- WET-2-SAVE backings redesigned for low temperature resins and aqueous binders supporting a more responsible process
✅ Integrating Circularity
New prototypes with recycled components help advance circular solutions in abrasives.
#5 VALUE CHAIN ENGAGEMENT
Imerys holds its suppliers to the highest standards:
✅ Compliance with ESG standards and local regulations
✅ Commitment to workplace safety
✅ Alignment with the UN Sustainable Development Goals
Suppliers who fail to meet environmental and social responsibility standards are excluded from their supply chain. This rigorous approach ensures an ethical and resilient supply chain.
Imerys’ commitment to sustainability goes beyond just compliance – it’s about fostering long-term, responsible partnerships that make a real impact across its entire value chain.
#6 SUSTAINABLE PRODUCTS
Innovation and responsibility go hand in hand. Tyrolit designs new products and applications by integrating strict guidelines for sustainable development.
✅ Carbon footprint reduction:
Installation of photovoltaic panels, exploration of alternative solutions such as geothermal energy or wood-based gas. Infrastructure optimization has already led to a reduction of -1,100 tons of CO₂ per year.
✅ Commitment to local well-being:
Noise and odor reduction to improve quality of life for employees & locals.
#7 BONUS
Small actions, big impacts!
✅ Act for biodiversity
Samedia installed beehives at its production site to support pollinators and raise awareness.
✅ A 130% green factory
InterAbrasiv’s solar panels now produce 130% of their electricity needs!
So, what’s next?
These initiatives prove that CSR-driven innovation is reshaping the abrasive industry. The SEAM label is already guiding industry leaders toward the practices that will define the next decade.